Small Changes, Big Differences - Part 2
- Manfred Ewikowski
- Jan 17, 2024
- 6 min read
Updated: Jun 5, 2024
"A relatively small number of changes to the remuneration of workers, labour distribution and fuel sources can significantly improve the quantity and quality of brick production."
This blog is the final blog in the two-part series about how New Rivers Enterprises is working to make small changes that bring differences to the workers in Pakistani brick factories. We recommend reading the previous blog to get a complete understanding of this approach.
Brick Production Overview
Bricks which are made at the brick factories in and around Lahore in Pakistan are primarily classified into three categories. Class A+ and Class A bricks are the top grade bricks which can be used for a number of purposes including construction. Class B bricks are a second grade brick which is not always conducive for construction applications but can be used for non-load bearing purposes. Finally, Class C bricks are low grade bricks which are generally broken up to be used for road works and footings.
The changes proposed in this blog are aimed at increasing the percentage of Class A brick produced within the brick factories in the Punjab state in Pakistan. Currently, these factories produce about 50% Class A+ and A bricks, 25% Class B bricks, and 25% Class C bricks. By implementing the following simple changes the production percentage of top grade bricks will increase. As a consequence, the revenue of the brick factory will also increase.
Current Processes
It is important to understand the current production methods used to then appreciate the benefits of the simple changes New Rivers will implement. Generally, labour is divided into slave family groups rather than the stages required to produce bricks. Typically, one family is responsible for the production of 1000 brick units. These units are based on the quota of bricks a family is expected to produce in a given day. Each family is responsible for and paid only for the bricks they have made.
There are 6 stages involved in the production of bricks.
Mixing the clay used to make the bricks. Currently, each family mixes enough clay at the beginning of each day to form between 1000 and 1500 bricks.
Forming bricks using a mold.
Sun drying the bricks.
Moving sun-dried bricks to the brick kiln and then stacking them in the kiln. The areas where the bricks are dried are typically within 500m from the brick kiln.
Baking the bricks through a firing process. The typical fuel source for the brick kilns is a combination of firewood and low-grade coal.
Moving the baked bricks from the kiln to a storage area or directly to the customers who have pre-purchased them.
The first four stages of brick production are typically done by one family. The firing of bricks is a more specialised skill which is often done under the oversight of a kiln manager. Moving bricks out of the kiln can also be done by individual families. At any given time, thousands of bricks allocated to a family will be spread across the various production stages. Families are only paid for bricks which have completed the entire production process. Therefore, payment is generally only received for 3000 to 4000 bricks per week despite the families working 7 days per week. The payment rate per 1000 bricks is approximately 1,100 rupees (around US$4.00).
This division of labour is a simple means by which the managers of the brick factories can allocate payment for the bricks produced by each family. Shortfalls in production and any losses incurred by the factory can also be allocated to individual families by increasing the amount of their debts.
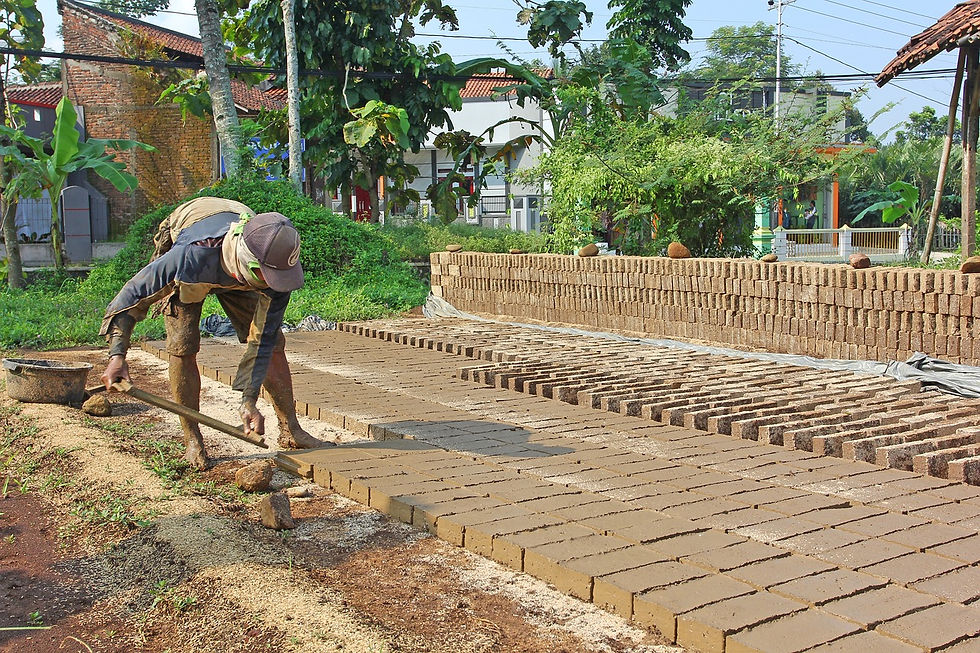
Remuneration Restructure
The debts which enslave the workers of brick factories will be included with the purchase of any brick factory operated by New Rivers. These debts are forgiven as soon as the transfer of ownership has been completed. Alternatively, when New Rivers rents a factory it pays the debts owed to the factory owner which then transfers ownership of the families to New Rivers. Of course, we do not enforce these ownership rights so these families can choose to remain at the factory (under dramatically improved working conditions) or leave the factory. The costs to purchase these debts are absorbed as operational expenses. The following changes, in addition to the changes proposed in the first blog, are made to encourage the workers to continue working at the factory.
Each family receives a daily income of at least 1,500 rupees (around US$5.50). At least another 500 rupees are daily credited into a fund which can be accessed by the family as needed. In this way, each family will receive at least 2,000 rupees/day (around US$7.25) when both parents continue working at the factory. Families in a New Rivers brick factory, will earn significantly more than they would under their previous payment structure.
Daily meals will also be provided to all the workers and the families of living at factory.
Children will not be permitted to work any stage of brick production.
Worker’s children will be offered education at schools operating at the brick factories with the aim of transitioning them to mainstream education once they have caught up on their previously lost education. The education at New Rivers' schools will be provided at no cost.
Disabled or elderly family members will not be required to work any stage of brick production. They could assist, depending on their capacity, their families by cultivating crops on the land gifted to them by New Rivers (see Part 1 of this blog).
Work days will be limited to 10 hours.
Work weeks will be reduced to 5 to 6 days.
Workers will continue to receive income and alternative employment (ideally within other New Rivers businesses) during times when the weather is not conducive to brick production.
Housing will be provided to the workers and their families on the brick factories at no cost.
Division of Labour Restructure
Flowing from the remuneration restructure are changes to the division of labour within a brick factory. Labour can be moved between specific brick production stages as required since individual workers are no longer tied to the production of specific bricks.
A significant change to the production process involves increasing the amount of clay mixed at one time. Teams of workers will mix large batches of clay each day, eventually with mechanical assistance. This approach will allow for greater control over the quality of the clay mix as consistent ratios of clay, salt and water can be maintained. Improving the quality of the clay will result in more Class A+ and A bricks being produced.
Secondly, the forming of the bricks will be done in larger teams. These teams will increase the coordination of the forming and distribution of the bricks in the sun-drying fields. During times of favourable weather, the size of the clay mixing and brick forming teams can be increased to maximise the number of bricks being sun-dried. Additionally, the inefficiency of separating the formed bricks by family groups will no longer be needed. This approach will result in less labour hours being required to form the same amount of bricks using the current processes.
Thirdly, a team can move sun-dried bricks into the kiln without disrupting the brick forming stage. When required, such as when rain is anticipated, these teams can be increased. The more efficient transfer of sun-dried bricks to the kiln will reduce losses resulting from rain damage. The redistribution of labour into teams will have similar benefits when it comes to moving baked bricks from the kiln.
The process for baking bricks would not be changed initially. The majority of the gains that can be made from this stage are not related to a redistribution of labour. These gains are made by redesigning the heat distribution and heat retention capacities within the kilns.
Rotating workers within teams will ensure a transfer of skills and knowledge and will reduce the risk of injuries associated with repetitive tasks. A team-based distribution of labour will also result in gains in production quantity and quality which will more than off-set the cost associated with the remuneration restructure.

Alternative Fuel Source
Transitioning from low-grade coal to high-grade coal is a more economical approach to baking bricks. High-grade coal costs approximately twice as much as the lower-grade coal currently used in most brick factories. However, the ratio of bricks which can be baked per ton of coal is roughly 5:2 in favour of the high-grade coal. A transition to high grade coal will result in a reduction of the amount of coal required to bake the bricks which in turn reduces pollution. Additionally, the reduction of tonnage of coal required more than off-sets the higher cost of the high-grade coal.
Another benefit from using high-grade coal is the increased production of top quality bricks. Generally, low-grade coal is not able to bake bricks to a Class A+ standard. The use of high-grade coal can result in a production rate of 40% Class A+ bricks, 40% Class A bricks and 10% each of Class B and C bricks.
A relatively small number of changes to the remuneration of workers, labour distribution and fuel sources can significantly improve the quantity and quality of brick production. These improvements are additionally to transition from a slave-based workforce and better long term financial, health and educational outcomes workers in New Rivers factories will experience.
Join Our Mission:
For more information on how you can be part of this transition through your investment with New Rivers, follow this link to learn more and join other investors.
We are always interested in new ideas that people may have with respect to changes that can be made at the brick factories and any other businesses that New Rivers is involved in. We look forward to hearing from you - email us at info.newrivers@gmail.com.

Pictured: Manfred, Michelle (centre) and the New Rivers Team
Comments